 | Introduction
Copper is the preferred and predominant choice in the electrical industry because of its high conductivity, both electrical and thermal. In order to obtain the required properties, unalloyed high purity copper is almost always used. This article discusses the rationale for this choice, and pays particular attention to the underlying metallurgical principles. It is intended to serve as a technical discussion of pertinent developments spanning the past several decades in the copper wire industry.
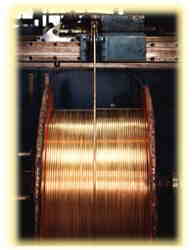 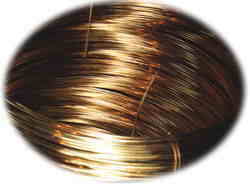
ASTM Specification Codes for Coppers and Copper Alloys
Copper or Copper Alloy Product
|
ASTM Spec |
Copper or Copper Alloy Product
|
ASTM Spec |
Hard drawn copper wire |
B1 |
Cu conductors for electronic equipment wire hookups |
B286 |
Medium hard drawn copper wire |
B2 |
Manganese brass (Cu-Zn-Mn) sheet and strip |
B291 |
Annealed copper wire |
B3 |
Silver coated annealed copper wire |
B298 |
Bronze trolley wire |
B9 |
Free cutting copper rod and bar |
B301 |
Free cutting brass rod, bar, and shapes for use in screw machines |
B16 |
Threadless copper pipe |
B302 |
Cartridge brass sheet, strip, plate, bar, and disks |
B19 |
Copper drainage tube (DWV) |
B306 |
Naval brass rod, bar, and shapes |
B22 |
Seamless Cu alloy pipe and tube |
B315 |
Bronze castings for bridges and turntables |
B22 |
Nickel coated annealed Cu wire |
B355 |
Copper alloy ingots |
B30 |
Cu and Cu alloy seamless condenser and heat exchanger tubes w/ fins |
B359 |
Tinned soft or annealed copper electrical wire |
B33 |
Hard drawn Cu capillary tube for restrictor applications |
B360 |
Standard sized seamless copper pipe |
B43 |
Cu-Ni alloy castings |
B369 |
Copper trolley wire |
B47 |
Cu sheet and strip for building construction |
B370 |
Annealed rectangular and square bare copper electrical wire |
B48 |
Cu-Zinc-Si alloy rod |
B371 |
Hot rolled copper rod redraw for electrical use |
B49 |
Seamless Cu and Cu alloy rectangular wave guide tube |
B372 |
Steam or valve bronze castings |
B61 |
U-bend seamless Cu and Cu alloy heat exchanger and condenser tubes |
B395 |
Bronze rough castings for locomotive wear parts |
B66 |
Cu-Ni-Si alloy rod and bar |
B411 |
Car and tender lined journal bearings |
B67 |
Cu-Ni-Si alloy wire |
B412 |
Seamless bright annealed copper tube |
B68 |
Cu-Al-Si-Co alloy and Cu-Ni-Al-Si alloy sheet and strip |
B422 |
Seamless copper tube |
B75 |
Gear bronze castings |
B427 |
Seamless copper water tube |
B88 |
Cu and Cu alloy clad steel plate |
B432 |
General purpose and pressure vessel Cu-Si alloy plate, sheet, strip, and rolled bar |
B96 |
Cu-Co-Be (UNS C17500) and Cu-Ni-Be (UNS C17510) rod and bar |
B441 |
Cu-Si alloy rod, bar, and shapes |
B98 |
Welded Cu tube |
B447 |
General purpose Cu-Si alloy wire |
B99 |
Cu foil, strip and sheet for printed circuits and carrier tapes |
B451 |
Rolled Cu alloy bearing and expansion plates and sheets for bridges and structural use |
B100 |
Leaded brass (Cu-Zn-Pb) rod |
B453 |
Lead coated copper sheet |
B101 |
Leaded brass (Cu-Zn-Pb) extruded shapes |
B455 |
Phosphor bronze plate, sheet, strip, and rolled bar |
B103 |
Cu-Fe alloy plate, sheet, strip, and rolled bar |
B465 |
Hard drawn Cu alloy wires for electrical conductors |
B105 |
Seamless Cu-Ni pipe and tube |
B466 |
Cu and Cu alloy seamless condenser tubes and ferrule stock |
B111 |
Welded Cu-Ni pipe |
B467 |
Fig. 9 deep section grooved and fig. 8 Cur trolley wire for industrial haulage |
B116 |
Seamless Cu-Ni pipe and tube |
B469 |
Leaded brass plate, sheet, strip, and rolled bar |
B121 |
Bonded Cu conductors for use in hookup wire for electronic equipment |
B470 |
Cu and Cu alloy forging rod, bar, and shapes |
B124 |
Cast Cu-Ni ship tailshaft sleeves |
B492 |
Cartridge brass cartridge case cups |
B129 |
Compact round concentric-lay-stranded Cu conductors |
B496 |
Commercial bronze strip for bullet jackets |
B130 |
Cu alloy continuous castings |
B505 |
Cu alloy bullet jacket cups |
B131 |
Cu clad stainless steel sheet and strip for building construction |
B506 |
Cu rod, bar, and shapes |
B133 |
Cu alloy strip for flexible metal hose |
B508 |
Brass wire |
B134 |
Cu-Co-Be alloy, plate, sheet, strip, and rolled bar |
B534 |
Seamless brass tube |
B135 |
Welded Cu and Cu alloy heat exchanger tube |
B543 |
Manganese bronze rod, bar, and shapes |
B138 |
Seamless and welded Cu-Ni tubes for water desalinization plants |
B552 |
Phosphor bronze rod, bar, and shapes |
B139 |
Light gage UNS C26000 brass strip in narrow widths for heat exchanger tubing |
B569 |
Leaded red brass hardware bronze rod, bar, and shapes |
B140 |
Cu-Be alloy forgings and extrusions |
B570 |
Aluminum bronze sand castings |
B148 |
General purpose Cu alloy sand castings |
B584 |
Aluminum bronze rod, bar, and shapes |
B150 |
Welded brass tube |
B587 |
Nickel Silver (Cu-Ni-Zn) and Cu-Ni rod and bar |
B151 |
Cu-Zn-Sn alloy plate, sheet, strip, and rolled bar |
B591 |
Cu sheet, strip, plate, and rolled bar |
B152 |
Cu-Zn-Al-Co alloy plate, sheet, strip, and rolled bar |
B592 |
Phosphor bronze wire |
B159 |
Welded Cu alloy pipe |
B608 |
Aluminum bronze, plate, sheet, strip, and rolled bar |
B169 |
High-strength, high-conductivity Cu alloy electronic wire |
B624 |
Cu alloy condenser tube plates |
B171 |
Cu and Cu alloy solar heat absorber panels |
B638 |
Rope lay std. conductors w/ bunch stranded members |
B172 |
Welded Cu and Cu alloy tube for AC/refrigeration use |
B640 |
Rope lay std. conductors w/ concentric stranded members |
B173 |
Seamless and type D welded Cu distribution tube |
B641 |
Bunch stranded conductors |
B174 |
Cu-Be alloy seamless tube |
B643 |
Brass die castings |
B176 |
Brass, Cu, and Cr plated pipe nipples |
B687 |
Cu bus bar, rod, and shapes |
B187 |
Cu, Cu alloy, and Cu-clad stainless steel sheet and strip for electrical cable shielding |
B694 |
Seamless Cu bus pipe and tube |
B188 |
UNS C69100 seamless Cu alloy pipe and tube |
B706 |
Lead Cu and Lead Cu alloy coated soft Cu electrical wire |
B189 |
Welded Cu water tube |
B716 |
Cu-Be alloy plate, sheet, strip, and rolled bar |
B194 |
Fine wire and rope-lay bunch stranded Cu electrical conductors |
B738 |
Cu-Be alloy rod and bar |
B196 |
Cu-Ni-Sn spinodal alloy strip |
B740 |
Cu-Be alloy wire |
B197 |
Seamless Cu tube coils |
B743 |
Nickel Silver (Cu-Ni-Zn) and Cu-Ni alloy wire |
B206 |
Cu-Zn alloy sheet and strip |
B747 |
Cored, annular, concentric- lay stranded Cu conductors |
B226 |
Sand cast Cu alloy for valve applications |
B743 |
Concentric-lay stranded Cu and Cu clad steel conductors |
B229 |
Cu-Co-Be alloy sheet and strip |
B768 |
Tinned hard drawn and medium hard drawn copper electrical wire |
B246 |
Round wire for use as grid side rods in electron tubes |
F9 |
Cu base alloy centrifugal castings |
B271 |
Wrought oxygen-free Cu for electronic devices |
F68 |
Cu flat wire and strip w/ rolled or drawn edges |
B272 |
Wrought electronic grade Cu alloys |
F96 |
Seamless Cu tube for air conditioning and refrigerator use
|
B280 |
General use nonferrous nuts |
F467 |
Cu and Cu alloy hot pressed die forgings
|
B283 |
General use nonferrous bolts, hex cap screws, and studs |
F468 |
Conductor Requirements
Considerable progress has been made in recent years to explain the electronic nature of the noble metals, i.e., copper, silver, and gold. These elements exhibit high conductivity because their conduction electrons show relatively little resistance to movement under an electric field. Copper in particular is an excellent conductor because outermost electrons have a large mean free path (about 100 atomic spacings) between collisions. The electrical resistivity is inversely related to this mean free path.
Several electrically conductive metals are lighter than copper, but since they would require larger cross-sections to carry the same current, are unacceptable if limited space is a major requirement (e.g., in small electric motors). Consequently, aluminum is used mainly when excessive weight could become a problem. Copper possesses the best characteristics for commercial applications, inasmuch as silver must be dismissed because of its prohibitively high cost.
Applications
Copper is one of the few metals that finds most widespread use in the pure form, rather than as an alloy. There are approximately four dozen different wrought alloys that contain a minimum copper content of 99.3 weight percent (and therefore designated as "coppers"), albeit only a handful are used industrially as electrical conductors. The most widely used of these dilute alloys is known as electrolytic tough pitch (ETP) copper, which consists of extremely high purity metal that has been alloyed with oxygen in the range of 100 to 650 ppm. ETP copper is not recommended for use in hydrogen environments due to its susceptibility to hydrogen embrittlement when exposed to these temperatures. Under these environmental environments, either oxygen-free (OF) or oxygen-free electronic (OFE) grades of copper should be used. Silver bearing copper (OFS) finds limited use in power transformers because of its higher strength and softening resistance at elevated temperature.
Production of Rod and Wire
Prior to the 1970s nearly all copper rod was made by a batch process, which included pouring and solidification of molten copper into special shaped ingots known as wirebars, reheating the bars in a slightly reducing protective atmosphere, and breaking up the cast dendritic structure by hot rolling in air to a rod form. This was followed by pickling in 10 percent sulfuric acid to remove oxides, and by butt welding of one end to another to form larger coil lengths. Today, a continuous casting and rolling process produces virtually all copper rod. Benefits of continuous casting include less microsegregation of impurities, reduction of copper oxide particles on the surface, fewer steel inclusions resulting from contact with mill rolls, almost total elimination of welds, and lower overall processing costs.
Oxygen is intentionally alloyed with copper to act as a scavenger for dissolved hydrogen and sulfur to form the gases H2O and SO2 in the melt. If the oxygen content is kept under control, microscopic bubbles form throughout, and under ideal conditions will offset the approximately 4% shrinkage in volume associated with the liquid-to-solid transformation. If the resulting pores are not too large, they are completely eliminated during hot rolling.
Most continuous casting and rolling units contain non-destructive equipment (eddy-current) that is used on-line to detect surface defects such as cracks and oxides. For certain high quality applications, several mils of metal are oftentimes removed from the rod surface by mechanical shaving.
Most round and square copper products are manufactured by wire drawing using either conventional manmade polycrystalline dies or natural single crystal diamond dies. Copper has excellent formability, and can be easily drawn from rod into very fine wire sizes without the need for intermediate process anneals. In spite of this desirable characteristic, common practice in the magnet wire industry is to limit the area reduction during drawing to about 90%, followed by an anneal. Beyond that level of reduction, metallurgical structure changes can occur which can degrade the wire’s mechanical properties. Magnet wire is often produced by the so called "in line process" which involves "slow" speed wire drawing followed in line by continuous annealing performed in tandem with enameling. The final wire products are improved appreciably by limiting the area reduction between anneals to about 90%.
Role of Impurities
Chemistry is one of the most important variables needed for the establishment of high electrical conductivity. The most harmful of these elements can significantly decrease electrical conductivity, increase the mechanical strength of the annealed wire, retard recrystallization, and will sometimes induce hot shortness during the hot rolling process in the production of rod. Numerous investigations have shown that very small additions of solute elements may increase the electrical resistivity (decrease conductivity) of copper in a linear manner as illustrated in Figure 1. Many impurities increase the half-hard recrystallization temperature in a non-linear relationship. However, the deleterious effects on conductivity are minimized when the impurities are tied up in precipitates or oxides rather than in solution.
Figure 2 shows the effects of various single element additions to a high purity ETP copper containing only 200 ppm of oxygen. In general, the first few parts per million of impurities have their greatest impact upon annealability compared with subsequent equal additions. However, it should be noted that the purity of commercial copper has improved dramatically since the electrical standards for copper, established in 1913, were represented by a conductivity of 100% IACS. Today, most commercial copper cathodes have conductivities approaching well over 101% IACS.
Influence of Oxygen Content
Oxygen is used as an alloying element to improve the soundness of "as-cast" copper bars through the control of gas-metal reactions. Equally important, oxygen acts as a scavenger in reacting with most of the impurities, which have their most potent effects on properties and annealing response when they are dissolved in the copper matrix. In contrast, harmful effects may be nullified when impurities are tied up as insoluble oxides. The maximum conductivity of ETP copper occurs at approximately 200 ppm of oxygen as shown in Figure 3. Consequently, oxygen content for ETP copper is generally in the range of 175 to 450 ppm. Lower oxygen values are usually avoided because of a propensity to hot cracking resulting from uncombined impurities. In contrast, oxygen values in excess of this optimum concentration range are not too common because of an adverse effect upon formability. Actual oxygen content is a compromise between attaining better (less sluggish) annealing behavior and avoiding possible drawability problems.
Importance of Thermal-Mechanical Process Variables
In addition to oxides formed from metallic impurities, equilibrium copper oxides can be made to either dissolve or precipitate from a copper matrix by altering the thermal history. These types of solid state reactions may also influence the final grain size because copper oxide inclusions help to promote a small uniform grain size during recrystallization. However, secondary recrystallization (abnormal grain growth) is associated with a duplex grain structure caused by the dissolution of oxides during a high temperature anneal. The propensity for grain coarsening and duplex grains is attributed to solution temperatures in excess of 500 C, and to oxygen concentrations less than 600 ppm. Some of these grain size results are exhibited in Figure 4. Coarse grains formed prior to wire drawing are not eliminated after the subsequent lower temperature anneals. The rate of cooling from high temperature can also influence the high temperature mechanical properties, particularly when the levels of impurities are high. Rapid quenching results in high, non-equilibrium levels of impurities in solid solution. On the other hand, slow cooling allows for the interaction between impurities and oxygen, which leads to subsequent precipitation from solid solution.
The amount of cold work by either wire drawing or rolling between intermediate process anneals is limited for commercial magnet wire. It is desirable to limit the amount of cold work prior to the final anneal in order to have good conformability (the ability of the wire to hold its shape during forming or winding with minimal springback). A high elastic modulus and low yield strength are desired properties because they are both indicative of minimum springback.
Annealing Behavior
Annealability of copper is a complex characteristic that is governed by large local inhomogeneities which can change with deformation and thermal history, metal purity, and oxygen content. Impurities play a much smaller role in affecting annealing behavior when they have precipitated, as opposed to being in solid solution. A correlation exists between annealing temperature and the atomic size difference between solvent (copper in this case) and solute (the impurity). Valence of a solute element is also an important parameter affecting annealability. However, due to the complexities associated with the thermodynamic interactions of multiple species, annealability cannot be simply related to such plausible parameters as atomic volume or valence of the solute.
Surface Effects
At ambient temperature, copper wire always contains a residual oxide film that originates from the hot, continuous-cast bar as it feeds into the hot rod rolling stage. It has now become standard practice in the copper industry to measure the residual surface oxide film thickness using a coulometric reduction test method. The oxide films can be quite deleterious, since they may lead to the generation of defects during drawing, excessive wear of drawing dies, inadequate solderability, and poor adhesion between the enamel film and the bare conductor.
Copper rod defects often time originate from the continuous casting and rolling process, and include slag and copper oxide inclusions, hot-cracks, slivers, fold-over of the as-cast bar corners, insufficient removal of scale, or coining of oxide particles into the rod surface. Most of the intermetallic inclusions are brittle, and act as sites for crack initiation and propagation in the as-drawn wire. With respect to defects, fine magnet wire and shaped wire are the most critical products to produce.
The largest single classification of surface defects originates from wire drawing, and occurs on the bare conductor surface as die marks, mechanical damage, gouges or slivers. Slivers formed because of wire drawing problems tend to be free from entrapped oxides. Surface damage is frequently caused by misalignment of the moving wire within the drawing machine or by the compaction of copper fines inside the throat of the wire drawing die.
Future Challenges
The demand for better surface quality and increased package size will continue to accelerate, and will place an even heavier emphasis on "defect free" rod and fewer wire breaks (i.e., superior drawability). The driving force for these requirements will be better energy efficiency, increased global competition, more household appliances, and smaller size motors where space is a premium, as for example, in automotive applications. Consequently, finer gage sizes will be used more often.
With the advent of electrowinning and continual improvements in electrolytic refining, the purity of current commercial copper cathodes appears to have reached an acceptable plateau, and there is presently no need for further reducing the impurity levels. In the free machining brass industry, however, bismuth is starting to be used as an alloying element for the replacement of lead. Since bismuth is extremely poisonous to electrical copper conductors (>1 ppm can not be tolerated), it is imperative that the brass and copper scrap streams be completely separated from one another.
A major concern facing the wire industry is the extremely high quantity of surface defects that are generated during wire drawing by abrasive or delamination wear. To help alleviate this problem, emphasis is being placed on improvements in rod surface quality, drawing lubricants, filtration of solid particulates, and production of synthetic single crystal diamond drawing dies.
An important future challenge is to develop more sensitive sensors for the non-destructive detection of defects on bar, rod, and wire using non-contact test methods. Many of the harmful surface defects are too small to be detected by the eddy-current inspection equipment used presently. In addition, on-line inspection equipment needs to be developed to easily detect the presence of macroporosity and other internal defects.
Factors affecting the properties, processing and performance of electrical copper conductors in wire form can be rationalized fairly well on the basis of existing metallurgical principles. However, the relationship between impurity level and both annealing temperature and electrical resistivity need to be refined further in a more quantitative manner.
Summary
Unalloyed pure copper, rather than its alloys, is used almost exclusively as electrical wire conductors. Oxygen is intentionally added in small quantities to control the impurity level and improve the electrical conductivity. Final properties and processing behavior are intimately related to impurity and oxygen contents, and can be adequately explained using basic metallurgical principles.
|  |